MAINTENANCE & QUESTIONS
1. CONDENSATION:
Below are actual pictures of condensation on the inside of a glazed Bilco door that we installed. Yes, this is normal.
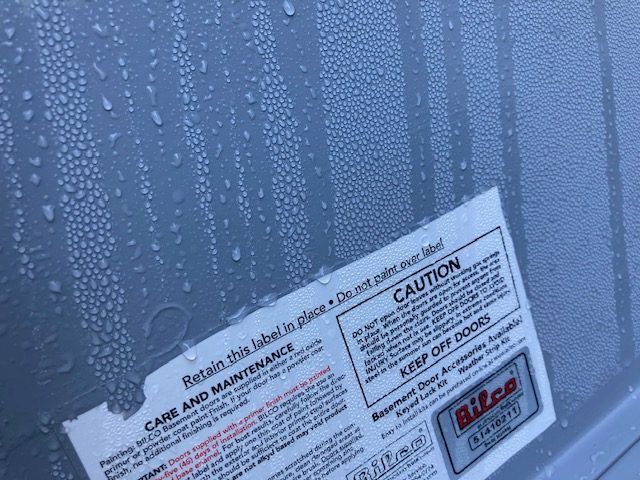

Dew or frost from condensation is most likely to happen in the mornings, especially in the Fall, and sometimes in the Spring. As a general rule, if there is dew or frost on your car windshield, chances are very high that there will be dew or frost inside the cellar door, and sometimes outside. Condensation will always be heaviest on metal parts where they are in direct contact with masonry, such as the side of a cellar door abutting a masonry landing and steps. When the air temperature falls below the dew point, there will be condensation. And since the air is colder than the metal, condensation is especially heavy. Here’s some info on dew point https://www.livescience.com/43269-what-is-dew-point.html Condensation cannot be stopped. It has been happening since before the dawn of human civilization, and will continue indefinitely. Condensation causes heavy rusting. Cellar doors usually rust faster on the inside than the outside. Paint does not stop the rusting problem, which is why we glaze them like a bathtub.
2. VENTILATION / AIR GAP BELOW FRONT DOORS:
This whole matter is directly connected with Point #1, condensation. Bilco, Steelway, and Gordon cellar doors are all designed to wick away the water, but allow air flow under the front of the doors to reduce condensation. It seems like every customer thinks moist air is flowing in. This is incorrect. Condensation occurs on the inside, and the moist air flows out under the fronts of the doors. When the doors close, and you look from the inside after you slide the lever into the closed position, you will see a tiny air gap. It is long and thin, and there’s a bit of light. That’s where the moisture escapes. It’s not an installation error, or a design flaw from the factory. It’s meant to be that way. Bilco increased the size of the air gap from its older models, to have more ventilation. The size of the air gap has to be big enough for adequate ventilation, but small enough to keep out mice. Those are the design parameters at the factory. The same ventilation concept exists with attics and new roofs. Roofing these days is installed with a ridge vent, gable vents, and roof vents. All three are to allow air flow. Below is a depiction of an attic showing ventilation and air flow.
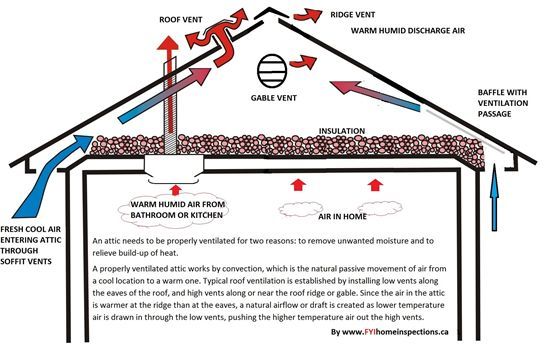
Lack of adequate ventilation on a cellar door has all the same issues and problems as a roof. In the case of our products, the situation is more extreme. There will be much more condensation under a cellar door than in an attic. Lack of ventilation causes:
- Heavier condensation and associated heavier rusting
- Mold & Mildew
- A bad stale air problem
- Excessive heat buildup in summer, if directly exposed to the sun
Bilco sells a rubbery gasket that can be installed to limit ventilation. Their own customer service representatives discourage people from buying it. We will not sell or install this gasket, because we don’t want our customers to have mold and mildew, and the other problems. Cellar doors must have air flow. You won’t have rust, because of how we glaze, but you will have the other problems if you limit the ventilation.
(3) CUSTOMER WANTS TO KEEP OUT BUGS. A new cellar door will not keep out bugs. They are not designed to keep out bugs. Bugs can come in under the front of the doors through the ventilation gaps. The entry door at the bottom of the stairs is the barrier to keep out bugs, if it is a modern door. That’s the door that has weatherstripping, and which closes snug with no gap at the bottom. You don’t have bugs coming in through your front door, or your kitchen door. Same concept.
(4) NOT A SOLUTION FOR BASEMENT TEMPERATURE: Customers wishing to keep their basement warmer should install a standard pre-hung exterior door at the bottom of the stairs, just like your front or side door. A Bilco / Cellar Door is not even part of the solution for basement temperature concerns. It’s made of a solid heavy steel. Steel conducts cold even more than aluminum, and it’s not insulated. When it’s 20 degrees outside, it will be 22 degrees under the new cellar door, and only because some warmth is radiating out of the basement through the lower door. We are advising customers upfront to set proper expectations. We are not losing business by educating customers. If your main concern is basement temperature, hire us to install a pre-hung exterior door at the bottom of those foundation stairs. When our work meets our customer’s real concerns, we both benefit, and establish a long-term business relationship.
(5) WHY DOES IT COME STANDARD AS AN UGLY RED COLOR: For cost reasons, a few customers pass on the glazing. All manufacturers sell them as pre-primed red. There’s iron oxide (finely powdered rust) in the primer as a key ingredient. That pushes the primer color in the rust-color direction, and it’s not economical to try and force another color into the product. They add a little extra red pigment so it’s not an actual rust color. The factory-red primer offers some protection against rust, but the manufacturers recommend they be painted, especially the underside, to resist rust.
(6) WHAT ABOUT FOUNDATION LEAKS: We can only guarantee that our cellar door will not leak where we anchor it with cement, and any new cinderblocks or bricks that we lay down will not leak. The foundation wall below our actual masonry work is not “part of the job”, or part of our warranty. Water could be coming in 3” below our work, 24” below our work, or even 7 feet below our work. And since we are not doing any masonry work there, if it was leaking before, it will leak again. Cracks below our work could continue to leak. We have, on occasion, taken a grinder to old cracks and widened them to 3/8” or ½”. And then we fill the gap with our hydraulic / anchor cement. Sometimes it works, sometimes it doesn’t. We are not basement waterproofing specialists, but it’s better than nothing. There are contractors who grind out cracks and install a special sealant, and others who install trench drains or apply basement waterproofing paint. We won’t be offended if you want to hire one for that phase of work, it’s not what we do. We have a basement waterproofing contractor who overlaps most of our service area that we can refer you to.
(7) HOW TO CLEAN: The glazing is quite durable, and almost nothing will scratch it. However, we recommend against using abrasive chemical agents or scrubbing with steel wool. A kitchen scrubby sponge with palmolive or similar products works just fine. A steel snow shovel will scratch a steel door, so be careful there. Plastic shovels should not cause damage. The glazing is a “gloss” finish, but in the future won’t look as shiny due to dust and pollen. In the event that there is a “ding”, they can be filled with Bondo and sanded smooth. Cellar doors are not meant for cars to drive on them, and could be dented.
(8) WHY WASN’T THE UNIT SANDED PRIOR TO GLAZING: The units are welded at the factory, or contain parts that are welded on. Sparks fly during the welding, which are tiny nodules and specs of molten steel that land on the bare steel and adhere. This is a production issue at the factory. The factory may be brushing some off while still molten, unsure. If they are, they aren’t getting them all. The surface isn’t perfectly smooth prior to dipping. The factory then dips the parts into a large vat of primer, and lets it dry. Any drips in the primer can be sanded down, but an orbital sander will not remove the specs and nodules that are made of steel. Trying to sand them down removes the factory primer that is essential, and that voids the factory warranty. And then the imperfections in the steel are still there. Also, if bare steel is painted or glazed without the factory primer, the paint or glaze will fail.
(9) WHY CAN’T YOUR GLAZING BE SPRAYED ON: There are four reasons for this. (1) It can be brushed on, but once the product is aerosolized (turned into a tiny mist), it is classified as an environmental pollutant. (1) Dept. of Environmental Protection permitting in New Jersey is an impossible obstacle to commercial spray-coating for a business our size. The time, the effort, and the cost (reportedly over $200,000) mean it is simply not going to happen. The fines for doing it anyway without permits start at $100,000. (3) Going through all the DEP permitting, and then buying a building and setting up an industrial spray operation where zoning permits it would result in our prices not being affordable. Note how much auto body work has gone up over the past 25 years. A lot of that increase has to do with environmental regulations for spray coating, and the rising cost of automotive paint ($900+ a gallon), also due to regulations. (4) Our industrial coating, brushed on, is thicker and more durable than it would be if sprayed on.
Due to all these reasons, the industrial glazing has to be brushed on. It’s going to be 100 times more rust-resistant than any paint, and it’s an excellent product. It looks incredible from 5 feet away. From 5 inches away, you might see brush marks, especially in the darker colors. Black is by far the most difficult color, and Iron Ore isn’t far behind.